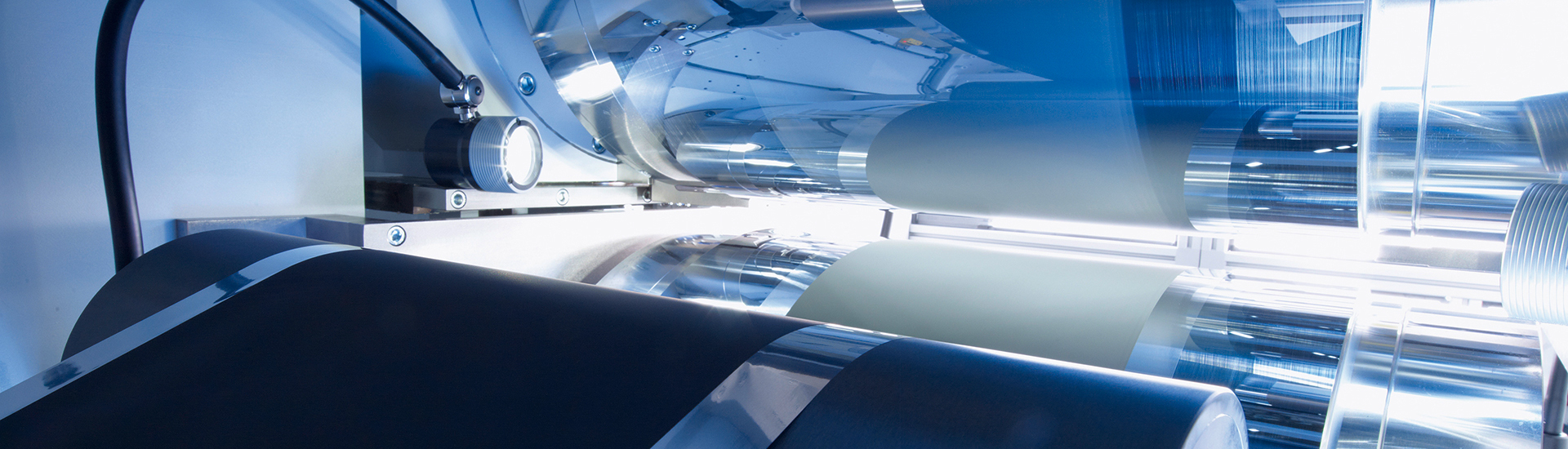
Gap control
The patented gap control on the BREYER calender enables a gap and force mode of operation. As an option, closed-loop thickness control can be selected.
You can switch between the two modes on the fly. This can be set precisely by measuring the actual value of the gap. The line forces that can be achieved are up to 3800 N/mm. Electrodes with continuous or intermittent coating can be processed.
Power-saving pressing
Thanks to the special non-stop roll positioning system, the hydraulic pressing force is transferred to the substrate surface with almost no loss. This allows you to work with the lowest possible pressing force, which minimizes the distortion of the electrode track.
Direct flow of power – the advantageous BREYER principle.
With the BREYER calender technology, the power flow runs directly via the roll onto the coating. The force and the product thickness can be set in a defined manner.
For comparison – the only indirect power flow in conventional calenders. In conventional calenders with mechanical adjustment systems between the rolls, part of the force is diverted via the adjustment system and therefore does not reach the product surface. Higher line forces are necessary. Bearing and machine are more heavily loaded. Adjusting the product thickness is usually difficult.
High-precision calender gap control. New closed loop thickness control with inline thickness measurement
For more than 30 years, BREYER has been setting standards with hydraulic nip control in calenders. This technology allows the gap to be adjusted quickly and reproducibly without mechanical adjustment mechanisms.
Calender for lithium electrodes. Adjust faster - save costs.
A newly developed gap control system is used in calenders for the production of electrodes for modern lithium batteries. It works on the closed-loop principle, i.e. the gap between the two rolls is constantly measured by high-precision sensors and compared with the target value set on the HMI.
The operator can therefore adjust the calender gap in a matter of seconds. This is a must for electrode production, where every metre of the high quality and expensive material is important.
Better product tolerances
Standard equipment always includes the option to calibrate in either force or position mode. This allows the optimum method to be selected for the electrode type.
In addition, the high-precision sensors measure concentricity. Irregularities are detected and compensated for by the electro-hydraulic control system, ensuring maximum product tolerance.
Manual corrections between the left and right sides of the roll are also possible and can be entered using appropriate correction factors.
In production, product tolerances of less than +/- 1.5 µm are possible.
Closed loop thickness control
The new IONPress 800 calender generation features even more advanced and faster power electronics, enabling outstanding quality when calendering electrode films over flexible product thicknesses.
In conjunction with a traversing thickness gauge with chromatic confocal measurement technology, it is now possible to implement optional closed-loop thickness control. This allows the desired product thickness to be precisely achieved without operator intervention. The closed-loop control automatically adjusts the gap position/gap force depending on how far the desired product thickness is from the actual product thickness. The actual product thickness is measured inline by the thickness gauge to an accuracy of +/- 1 micron.
This means that not only can the desired product thickness be achieved in a matter of seconds, but also that the desired, varying product thicknesses can be guaranteed fully automatically, without having to manually determine the required machine settings.
The special feature: The operator can set the desired thickness of the calendered electrode film in precise 0.1 µm increments.
Closed-loop control thus guarantees an unprecedented form of quality assurance at the highest quality level.
The closed-loop control between roll gap and material thickness is a world first for Breyer calenders.
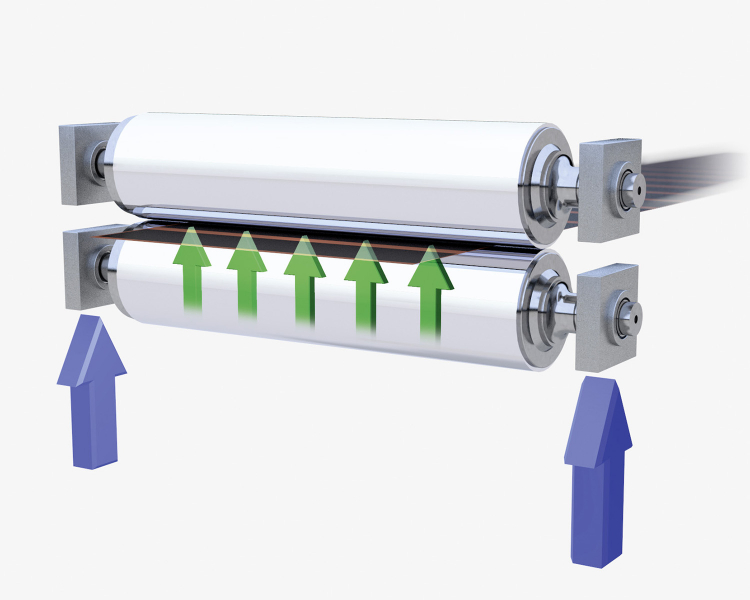
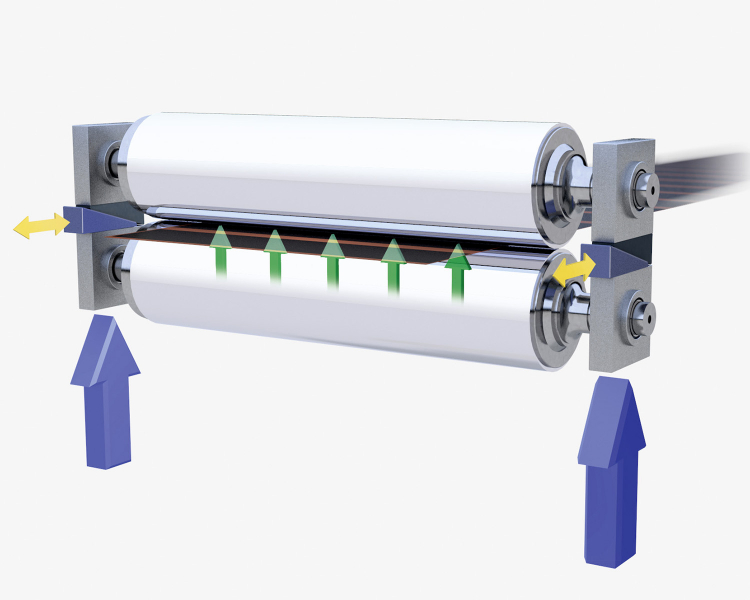